The **sand casting process** is a foundational method in the manufacturing industry, particularly valued for its versatility and cost-effectiveness. This technique involves creating metal components by casting molten metal into sand molds. Over the years, the process has become widely adopted in diverse industries, including automotive, due to the multitude of benefits it offers over other manufacturing techniques.
One of the primary **benefits of sand casting** is its ability to handle complex shapes and sizes that other casting methods may find challenging. This makes it particularly suitable for producing parts like the automotive transmission system, where precision engineering and efficiency are paramount. The materials used in sand casting are predominantly silica sand, clay, and water, which are molded around a pattern of the desired shape, creating a negative impression to house the molten metal. The sand casting materials are key to ensuring the quality of the final product, providing the necessary durability and stability.
However, like any other industrial process, sand casting is not without its challenges. **Sand casting defects**, such as shrinkage, porosity, and surface imperfections, can occur, but with advanced techniques and vigilant quality control, such issues can be minimized. Understanding **how sand casting works** allows manufacturers to optimize the process, ensuring that components such as the cutting-edge automotive transmission system are crafted with precision. This precision is crucial in automotive applications, where the seamless integration of parts can significantly impact performance and fuel efficiency.
When comparing **sand casting vs metal casting**, the former stands out for its economical nature, especially in producing small-batch items or prototypes. Additionally, the sand casting techniques have evolved substantially, allowing for enhanced accuracy and surface finish, making it a viable alternative for parts previously restricted to metal casting methods. This adaptability is a testament to the sand casting process's enduring relevance in industries focused on innovation and efficiency. Types of sand casting include green sand casting, dry sand casting, and shell mold casting, each offering unique benefits depending on the specific requirements of the product.
In conclusion, the sand casting process continues to play a significant role in the production of vital components such as automotive transmission systems. This process not only supports the demand for high-quality, durable parts but also aligns with the industry's pursuit of balancing power and economy through advanced technology. As manufacturers strive for excellence, the incorporation of modern **sand casting techniques** enhances their ability to deliver sophisticated and functional products, embodying the future of automotive technology.
No data
砂型鋳造技術:複雑な設計のための最新の方法
最新の価格を取得します >
Label | Value |
---|---|
ブランド | LSカスタムパーツメーカー |
カスタマイズサービス | 金属鋳造, 砂型鋳造, 低圧鋳造, 高圧鋳造, インベストメント鋳造 |
描画形式 | 2d/(pdf/cad)、3d(iges/step/glb) |
材料能力 | アルミニウム、真鍮、銅、銅、硬化金属、貴金属、ステンレス鋼、合金、TPR |
サンプル | 無料 |
供給能力 | 1日あたり100000個 |
表面仕上げ | カスタマイズされた仕上げ |
厚さ | カスタマイズされた厚さ |
タイプ | ブローチ/掘削/エッチング/化学機械加工/レーザー加工/ミリング/ターニング/ワイヤーEDM/ラピッドプロトタイピング/その他の機械加工サービス |
サービス | CNCの機械加工、金属鋳造、射出成形、板金製造、迅速なプロトタイピング、3D印刷 |
同様の製品を見つけます
製品説明
レビュー
接触
LS Manufacturingで次のプロジェクトを開始する準備はできましたか?
私たちのサービスと、あなたがあなたの目標を達成するのをどのように支援できるかについて詳しく知るために、今すぐお問い合わせください。
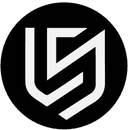
わずか1営業日から始まる急速なリードタイム。
ISO 9001、ISO 14001、IATF 16949およびAS9100D認証。
50以上の表面仕上げオプションを備えた100を超える材料が利用可能です。
費用対効果の高い大量生産。
1ピースの低い注文。