With the rapid development of science and technology,CNC machiningtechnology is also constantly evolving and upgrading. From the initial simple CNC system to today’s highly integrated and intelligent CNC machine tools, every technological leap has brought about a huge improvement in processing capabilities. It not only makes the processing process more efficient and precise, but also greatly broadens the boundaries of the processing field, making it possible to process complex parts that were unimaginable in the past. Therefore, when we stand at the intersection of this era, review the development history ofCNC machining, and look forward to its infinite possibilities in the future, I believe everyone can’t help but ask: What is CNC machining? This article will take you into the world of CNC machining and explore its mystery and charm.
What is CNC machining?
CNC (computer numerical control) machining is a manufacturing process that uses computer-controlled machines to remove material from a workpiece and shape it into the desired shape. In short, it is an advanced process method that uses digital information to control machine tools to achieve parts processing. It breaks the limitations of traditional processing methods, perfectly integrates human wisdom and the power of machines, and realizes automation, intelligence and precision in the processing process. In this era of information explosion and rapid technological changes,cnc-machining is not only an important cornerstone of Industry 4.0, but also a bridge connecting the past and the future, tradition and innovation.
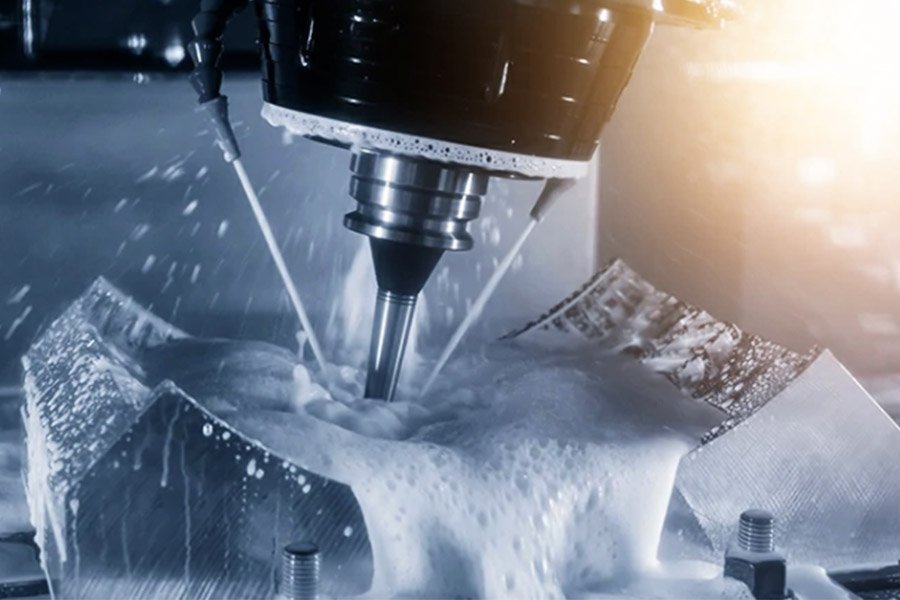
How does CNC machining work?
TheCNC machining processinvolves multiple steps, each of which is critical to achieving the desired result. Here’s how it works:
Step 1: Create a CAD drawing
The first step in the CNC machining technology process is to sketch the concept of the machined part on paper. However, we use precision machining CAD software designed for two-dimensional (2D) and three-dimensional (3D) modeling. The CAD drawing should be a to-scale model that provides information on inherent parameters such as thickness, depth, and other dimensions.
Step 2: Convert from CAD to CAM model
Convert CAD models to CNC code (G-code) using CAM (Computer Aided Manufacturing) software. This code instructs the machine how to move and cut.
Step 3: CNC machine configuration
In this step, the CNC machinist sets up the precision machine to execute the programmed G-code and M-code. It involves preliminary checking of machining input parameters and fixing the workpiece on the CNC machine.
Step 4: CNC machinist executes program
Nowadays,cnc machine workingmainly by entering a code to start manufacturing and moving accordingly. Remember, CNC machining technology is automated and won’t stop until the machinist presses the stop button. Therefore, the operator must remain vigilant during observation in case of sudden errors, emergencies, or situations requiring adjustments.
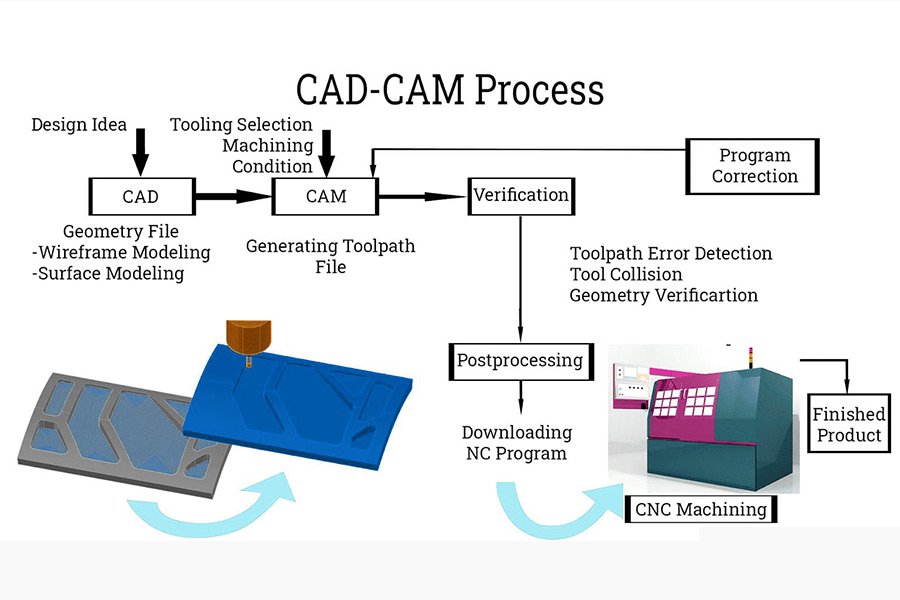
What are the types of CNC machining?
1.Grinding Machining
Grinding machiningis a processing method that uses abrasive tools (such as grinding wheels, whetstones, etc.) to grind the surface of the workpiece. The basic principle is to remove material on the surface of the workpiece through friction, scoring and scraping between the grinding tool and the surface of the workpiece to achieve the required size, shape and surface quality.
Grinding machining is widely used in machinery manufacturing, especially where high precision and high surface quality are required. It can process internal and external cylindrical surfaces, conical surfaces and flat surfaces of various workpieces, as well as special and complex forming surfaces such as threads, gears and splines. In addition, grinding can also process materials that are difficult to process with other machine tools, such as hardened steel, carbide, glass, ceramics, etc.
2.Lathe Machining
The basic principle oflathe machining is to use lathe equipment to remove excess material from the workpiece by rotating the workpiece and making it move relative to a fixed or moving cutting tool (such as a turning tool) to obtain the required shape, size and surface quality. parts or workpieces. Lathe machining can complete a variety of processing tasks, including but not limited to outer circle processing, inner circle processing (such as boring), end face processing, grooving, cutting off, forming surface processing, etc.
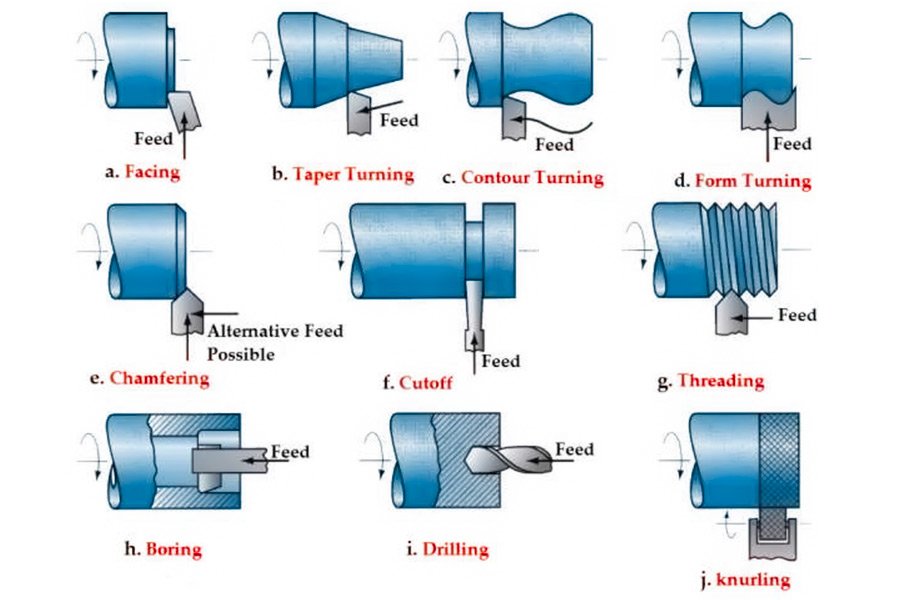
3.Milling Machining
Milling is the process of cutting material from a workpiece using a rotating tool to create the desired shape and size. The selection of cutting tools and the setting of processing parameters have a significant impact on the processing effect. Generally speaking, high-speed steel tools are suitable for milling most metallic materials, while carbide tools are suitable for harder materials. In addition, the settings of parameters such as cutting speed, feed amount and cutting depth also need to be reasonably selected based on specific materials and processing requirements.
Milling Machiningis suitable for workpieces of various materials and shapes, including flat surfaces, grooves, spiral surfaces, tooth surfaces, formed surfaces and outer circles, etc. In mass production, in addition to processing long and narrow planes,mill machiningcan almost replace planingand become a common method for processing planes, grooves and formed surfaces.
Compare the differences and advantages of milling machines and lathes
Milling Machines VS Lathes
Milling machine | Lathes | |
Processing method | The milling machine uses a rotating milling cutter to cut the workpiece fixed on the workbench or fixture. | The lathe rotates the workpiece so that the tool fixed on the tool holder can cut the workpiece. |
Processing object | Milling machines are mainly used to process flat surfaces, inclined surfaces, grooves, toothed parts (such as gears, spline shafts), spiral surfaces and various curved surfaces. | Lathes are mainly used to process various rotary forming surfaces, such as internal and external cylindrical surfaces, internal and external conical surfaces, internal and external threads, end faces, grooves, knurling, etc. |
Structural features | Milling machines usually have multiple axes, which can realize multi-axis simultaneous processing and are suitable for processing complex curved surfaces. | The structure of the lathe is relatively simple, and processing is mainly achieved through the rotation of the workpiece and the feed of the tool. |
Tool movement | In a milling machine, the tool rotates and the workpiece is fixed or moved. | In a lathe, the workpiece rotates and the tool is fixed or moves along the axis of the workpiece. |
Advantages
Advantages of milling machines
Wide processing range:Milling machines can process workpieces with various shapes and features such as planes, slopes, grooves, etc., and are especially good at processing complex curved surfaces and special-shaped parts.
High precision:Controlled by a CNC system,the machiningand milling machine is suitable for high-precision processingto meet the needs of precision manufacturing.
High flexibility:The multi-axis linkage function enables the milling machine to flexibly respond to various processing needs and improve production efficiency.
High production efficiency:Milling machines usually use multi-edged tools for cutting, which has high cutting efficiency and can shorten the processing cycle.
Advantages of lathes
Suitable for mass production:Lathes are particularly suitable for single-piece small batch and mass production, and can quickly complete the processing of rotary parts.
High processing accuracy:The lathe can achieve high processing accuracy through the rotation of the workpiece and the precise feed of the tool.
Strong versatility:The lathe can process a variety of rotating body surfaces, such as internal and external cylindrical surfaces, conical surfaces, etc., and has strong versatility.
Good economy:Themachining latheis relatively simple and has low maintenance costs. It is suitable for use by small and medium-sized enterprises and processing workshops.
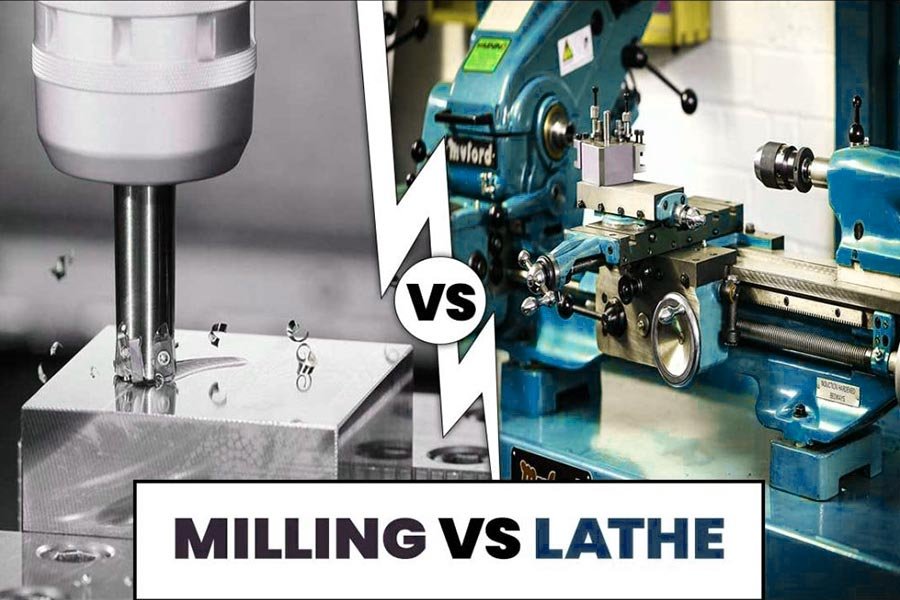
Why use CNC machining?
CNC machining offers many advantages over traditional manufacturing processes. Here are some of the main advantages of using CNC machining:
1.Accurate and controllable
One of the most important aspects of the manufacturing process is accuracy. It is unacceptable if a product is produced with defects or parameters outside established specifications. Because CNC machines are programmable, every detail of the production process is controlled.CNC machines can make identical parts without any errors. Reducing errors also eliminates unnecessary waste and makes it more difficult for others to copy your precise processes and designs.
2.Rapid production
CNC is ideal for manufacturing because of its efficiency. Once programmed by a CNC operator, the process of manufacturing parts and products can be automated, increasing the speed of operations.Unless your machines need maintenance, you don’t even need to shut them down. You can continue production without interruption, which is more efficient than using human labor.
3.Precision manufacturing
In a manufacturing environment, CNC machines play a vital role. Manufacturing encompasses a series of processes from product to customer, with each stage requiring different types of equipment and technology. During the manufacturing process, a variety of operations are required, including but not limited to welding, flame cutting, drilling, and shearing. During these operations, it is necessary to accurately position parts and quickly move the workpiece to a designated position and perform specific actions. All these tasks can be completed on CNC machines in a safe, efficient and precise manner.
4.Safe and reliable
In the context of manufacturing, human workers have always occupied an irreplaceable position. There are many factors you need to consider during the manufacturing process. You expect your work environment to be kept within the safest possible limits. If you are an occupational safety officer or engineer, share these tips with your colleagues. Eliminating certain human errors when producing small parts can reduce common risks that can cause serious injury. Doing so not only enhances the overall safety of your operations, but also provides your employees with additional time to complete other critical tasks.
5.Reduce costs
CNC machining technology is a cost-effective and precise method of producing parts and products. In modern industry, it is widely used in the machining of various precision and complex-shaped parts. Compared with traditional processing methods, the amount of raw materials required for CNC processing is also reduced. Due to the adoption of new technologies, production costs are reduced and productivity can also be increased. Focusing the shop floor on CNC technology can significantly reduce errors, production costs and product overhead.
What are the applications of CNC machining?
1.Aerospace industry
In the aerospace industry, CNC machining technology is widely used in the processing of high-precision, complex-shaped parts. Some common components include turbine blades, engine components and structural parts. CNC machining technology can meet the needs of high precision, high efficiency and high stability in the aerospace field and promote the continuous progress of aerospace technology.
2.Auto industry
In the automotive industry, CNC machining technology also plays an important role. It is widely used in the processing of automotive parts, including: engine components (cylinder block, cylinder head, crankshaft, connecting rod, etc.), transmission system components (gears, shafts, transmission housing, etc.) and body and chassis components (part of the body structure Parts and chassis parts) With the rapid development of the automobile industry and consumers’ increasing requirements for automobile performance, the application prospects of CNC machining technology in the automobile industry will be broader.
3.Electronic products
In the field of electronic product manufacturing, CNC machining technology also occupies an important position. It is mainly used for processing circuit boards, housings, connectors and other components. Specific applications include: circuit board processing, housing manufacturing and precision parts processing. CNC processing technology can realize efficient and high-precision processing of electronic product parts and meet the needs of continuous upgrading of electronic products.
4.Medical Industry
In the medical industry,CNC machining technology is widely used in the manufacturing of medical equipmentand the processing of medical implants.
CNC processing technology can meet the medical industry’s requirements for high precision and high quality in the processing of components for artificial joint replacements such as hip and knee joints, spinal internal fixators, dental restoration materials such as dental implants and crowns, and medical imaging equipment such as MRI and CT. The demand for medical equipment and implants improves the level of medical care and service quality.
5.Mold manufacturing industry
The mold manufacturing industry is one of the important application areas of CNC machining technology. The application of CNC machining technology in mold manufacturing mainly includes the processing of injection molds, die-casting molds and other complex-shaped molds, the processing of mold standard parts such as guide posts, guide bushes, and ejector pins, and the repair and transformation of molds that are damaged or need to be modified, etc. etc., the application of CNC machining technology has improved the accuracy and efficiency of mold manufacturing, reduced manufacturing costs, and promoted the rapid development of the mold manufacturing industry.
6.Energy Industry
In the energy industry,CNC machining technology is also widely used in the processing of various equipmentand parts. Such as the processing of key components such as pressure vessels, heat exchangers, pipelines, and the processing and manufacturing of oil drilling rigs, drilling tools and other equipment. The application of CNC machining technology in the energy industry has improved the processing accuracy and efficiency of equipment and components, and promoted the energy industry. sustainable development.
What does a CNC machinist do?
CNC technicians play a vital role in the manufacturing industry, responsible for utilizing computer numerical control (CNC) technology to control machine tools for precisemachining cnc.
Programming
CNC machinists need to use professional programming software (such as CAM software) to write CNC programs based on product drawings, CAD models, or engineers’ requirements. Before loading the program into the CNC machine tool, simulation software is used for verification to ensure the correctness and safety of the program. During the actual machining process, debugging and optimization are performed to ensure that the machine tool processes as expected.
Machine operation
CNC machinists are also responsible for pre-startup inspections of machine tools, including installing tools and fixtures, and adjusting various parameters of the machine tool to ensure that the machine tool is in optimal condition. During the processing process, the operating status and processing quality of the machine tool are continuously monitored, and the machine tool and cutting parameters are adjusted in a timely manner to ensure the stability and accuracy of the processing results. During the operation of the machine tool, if problems such as tool collision and processing errors are encountered, the problem can be quickly diagnosed and necessary repairs can be made.
Maintain
In accordance with the specifications of the equipment instruction manual and operating manual, perform daily maintenance, maintenance and cleaning of the machine tool, including checking the lubricating oil level, coolant volume, air pressure, etc., to ensure the normal operation of the machine tool. According to the maintenance plan of the machine tool, perform more in-depth maintenance work, such as cleaning the heat exchanger filter, checking the tool pull bolt, checking the mechanical origin of each axis, etc., to extend the service life of the machine tool. Organize and archive machine tool related information, including maintenance records, troubleshooting records, etc., to provide reference for subsequent use and maintenance of machine tools.
Factors to Consider When Choosing a CNC Machining Services Company
There are several key factors to consider when choosing a CNC machining services company. These include:
1.Processing capabilities and technical level:For an enterprise, the ability and technical standards to handle CNC processing matters are extremely critical. For example, Jusheng is widely praised for its superior manufacturing processing capabilities and technical expertise.
2.Technical strength and experience:In order to ensure that our enterprise has rich technical strength and experience, the company must form a professional team of experienced engineers, programmers and operators who can handle various difficult processing tasks. By reviewing the company’s past success stories, we are able to gain a comprehensive understanding of its performance and accumulated experience in similar projects, allowing us to effectively evaluate its technical strength and service quality. With its rich experience and successful practices, Longsheng Company has demonstrated its strong position in this professional field.
3.Quality control system:In order to ensure the quality of processed goods, companies should build a complete quality control system, covering many aspects from quality inspection of raw materials, strict supervision of process flow to inspection of final finished products. Master the inspection tools and equipment used by the company to ensure that processing accuracy reaches the expected accuracy. Longsheng adopts cutting-edge inspection tools in its CNC machining process to ensure that each part meets stringent industry standards and greatly exceeds customer expectations.
4.Price and cost-effectiveness:The company’s quotation should be fair and transparent, there should be no hidden fees, and the price should be consistent with multiple factors such as the quality of the service, the accuracy of the manufacturing, and the time of delivery. After comprehensively weighing multiple factors such as price, quality, delivery time and after-sales service, we conducted a comprehensive analysis of costs and benefits and selected a cost-effective service provider. Longsheng provides customers with competitive prices, but this does not compromise the quality of the products.
5.Delivery time and after-sales service:Timely supply and efficient after-sales service are the core elements to ensure customer satisfaction. Longsheng has excellent performance in both aspects to ensure that customer needs can be met in a timely and efficient manner.
6.Company Qualifications:The company’s certifications and qualifications not only demonstrate the company’s professional capabilities, but also reflect strict compliance with industry standards. Longsheng’s qualifications further consolidate its reputation in the field ofCNC machining.

Choose LS to provide you with one-stop service
Obtaining high-quality machining services remains an essential goal for rapid production success. AtLS, we, as amachining mill, offer a full range of machining services to meet your machining needs – from initial roughing to final finishing.
With over 15 years of manufacturing experience, we handle CNC parts with tolerances up to 0.005mm, offering same day quotes and 72 hour delivery. We produce parts in various quantities over 80.00 pcs. Our goal is to provide the highest quality, most efficient metal parts processing services to our prototyping and volume production customers. From raw material control to product inspection, we always pursue excellence in quality to provide you with impeccable results. LS recognizes the importance of every detail in production, so we ensure products not only meet your expectations but exceed them in terms of quality and visual appeal. When looking for a reliable and professional roughing service provider, consider Longsheng as your trusted partner to achieve efficiency and excellence in your machining process.
FAQ
1.What is CNC machining in simple terms?
To briefly summarize, CNC machining uses pre-written CNC programs (such as G codes and M codes) to control the movement trajectory, cutting speed, feed amount and other parameters of the machine tool, thereby achieving precision processing of metals, plastics, wood and other materials. It is an advanced process method that uses digital information to control machine tools to process parts. It breaks the limitations of traditional processing methods, perfectly integrates human wisdom and the power of machines, and realizes automation, automation and precision of the processing process.
2.What does a CNC machinist do?
CNC machinists play a vital role in the field of CNC machining. They are mainly responsible for using CAM (computer-aided manufacturing) software to compile CNC machining programs, pre-start inspections of machine tools and daily maintenance ofCNC machine toolsbased on product drawings and process requirements. and maintenance work, etc. Their work is directly related to the quality of products and the production efficiency of the enterprise. Therefore, CNC machinists need to have solid professional knowledge, rich practical experience and good teamwork spirit.
3.Why use CNC machining?
The main reasons for using CNC machining are its high precision, high efficiency, flexibility, high degree of automation and wide range of applications. These advantages make CNC machining one of the indispensable and important technologies in modern manufacturing.
4.Is CNC machining easy?
CNC machiningis not an easy technology. It requires technicians to have high-precision programming capabilities, rich process knowledge, and equipment maintenance and troubleshooting capabilities. Only through continuous learning and practice can one master this skill and become an excellent CNC machining technician.
Summary
CNC machining is an indispensable manufacturing process in various industries and offers high precision, efficiency, and versatility. It has become an important means of modern machinery manufacturing and parts processing, and is widely used in various industries, promoting the progress and development of industrial production. With the continuous advancement and innovation of science and technology, CNC machining technology will continue to play an important role in the future, providing strong support for the transformation, upgrading and high-quality development of the manufacturing industry.
Disclaimer
The content on this page is for reference only. LS does not make any express or implied representation or warranty as to the accuracy, completeness or validity of the information. No performance parameters, geometric tolerances, specific design features, material quality and type or workmanship should be inferred as to what a third party supplier or manufacturer will deliver through the LS Network. It is the responsibility of the buyer seeking a quote for parts to determine the specific requirements for those parts.Please contact us for more information.
LS Team
This article was written by several LS contributors. LS is a leading resource in the manufacturing field, withCNC machining,sheet metal manufacturing,3D printing,injection molding,metal stamping, and more.