In the realm of precision engineering, the hydroforming process has emerged as a revolutionary technology that reshapes the way we view metal fabrication. With an increasing demand for complex and lightweight components, industries are turning to this method to achieve unparalleled versatility and efficiency. The main_keyword, hydroforming process, takes center stage in this discussion, offering a multitude of benefits and applications across various sectors.
The multi-stage expansion shaft developed by LS Hardware Tech Co., Ltd exemplifies the state-of-the-art use of hydroforming technology. With this process, intricate shapes can be formed with minimal material waste, producing strong, lightweight structures that meet the demands of modern engineering. The hydroforming process uses a high-pressure hydraulic fluid to shape ductile metals such as aluminum, stainless steel, and titanium into desired forms. This capability not only improves the quality of the components produced but also enhances the overall aesthetic appeal, as seen in the sophisticated design of LS's Multi-Stage Expansion Shaft.
Hydroforming applications are numerous and varied, spanning the automotive, aerospace, and even consumer electronics industries. In automotive manufacturing, hydroformed parts are prevalent in creating chassis frames, exhaust components, and structural elements that require both strength and reduced weight. Hydroforming technology facilitates the production of complex components that would be challenging to achieve with traditional stamping methods, making it an essential process in the arsenal of modern manufacturing.
The benefits of hydroforming are significant, beginning with enhanced material properties. The hydroforming process provides increased strength and structural integrity compared to conventional methods like stamping. This is achieved through the uniform distribution of material across the finished product, reducing stress concentrations and potential points of failure. Furthermore, hydroforming offers cost savings by minimizing material wastage and reducing the need for secondary finishing processes.
LS Hardware Tech Co., Ltd, under the leadership of founder Mr. Nick Zhang, is at the forefront of this innovative technology. With over 20 years of expertise in manufacturing high-precision parts, LS has become a trusted partner to over 5,000 clients across diverse industries. Their ISO 9001:2015 certification reflects a commitment to quality and efficiency, as exemplified by their cutting-edge hydroforming equipment. The company's capability to deliver prototypes and mass production parts positions them as a key player in the global market, providing essential components for sectors requiring high-performance solutions.
When comparing hydroforming vs stamping, several distinctions emerge. Stamping, while effective for simpler shapes, often suffers from limitations in complexity and waste management. The hydroforming process, however, excels in creating multidimensional forms while optimizing material use. This is particularly advantageous in sectors such as aerospace, where precision and weight reduction are critical. Additionally, hydroforming allows for seamless integration of features such as mounting points and holes, reducing the need for further processing steps.
Metal hydroforming is not only reshaping how components are designed but also enhancing the capabilities of manufacturers like LS Hardware Tech Co., Ltd. The seamless integration of processes ensures that each product meets the stringent requirements of industries such as automotive, medical devices, and consumer electronics. With the company's vast experience and advanced technological equipment, LS guarantees products that embody durability and sophistication.
In conclusion, the hydroforming process is a transformative technology that LS Hardware Tech Co., Ltd harnesses to produce superior high-precision parts. The innovative Multi-Stage Expansion Shaft is a testament to the potential of hydroforming applications, creating components that are both functional and visually appealing. With the backing of a company known for its commitment to excellence and innovation, industries worldwide can rely on LS to provide the manufacturing solutions required to stay ahead in a competitive market.
Revolutionizing Part Fabrication: The Hydroforming Process
Get Latest Price >
Label | Value |
---|---|
Brand | |
Customization Service | Blanking, Hydroforming, Deep Draw Stamping, Progressive Die Stamping, Metal Stamping |
Drawing format | 2D/(PDF/CAD)、3D(IGES/STEP/GLB) |
Material Capabilities | Aluminum、Brass、Bronze、Copper、Hardened Metals、Precious Metals、Stainless Steel、Alloys、TPR |
Sample | Free |
Supply Ability | 100000 Pieces Per Day |
Surface Finish | Customized Finishing |
Thickness | Customized Thickness |
Type | Broaching/Drilling/Etching / Chemical Machining/Laser Machining/Milling/Turning/Wire EDM/Rapid Prototyping/Other Machining Services |
Services | CNC Machining,Metal Casting,Injection Molding,Sheet Metal Fabrication,Rapid Prototyping,3D Printing |
Find Similar Products
Contact
Ready to start your next project with LS Manufacturing?
Contact us today to learn more about our services and how we can help you achieve your goals.
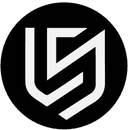
Rapid lead times starting from just 1 business day.
ISO 9001,ISO 14001,IATF 16949 and AS9100D Certification.
Over 100 materials available, with 50+ surface finish options.
Cost-effective mass production.
Order as low as 1 piece.
People who viewed this also viewed
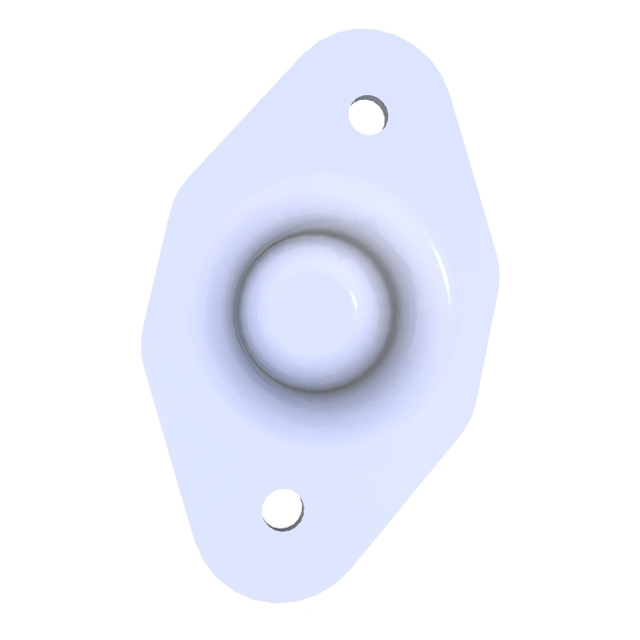
Exploring the Hydroforming Process: Advantages & Applications
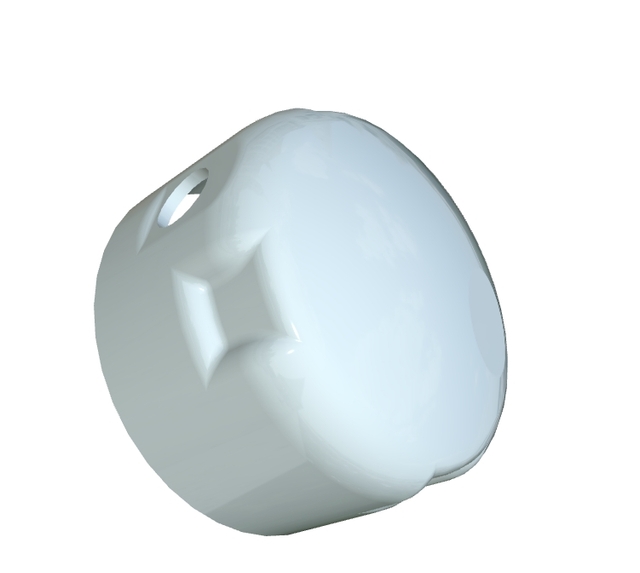
Revolutionizing Industries: Hydroforming Process Advantages & Applications
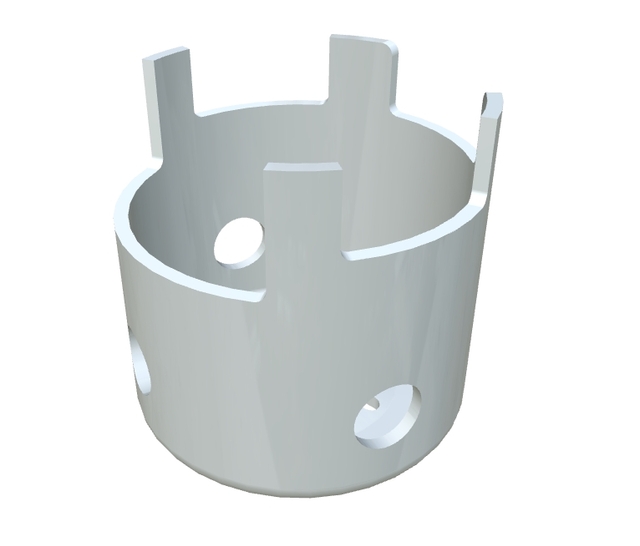
Revolutionizing Manufacturing with Hydroforming Techniques
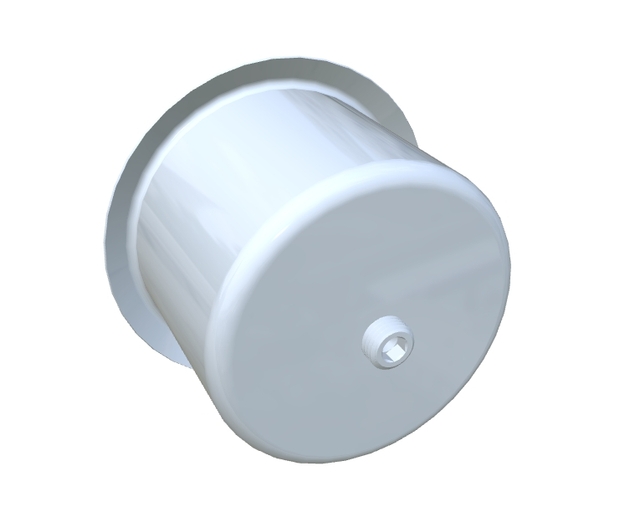
Exploring the Hydroforming Process: Applications, Advantages & Technology
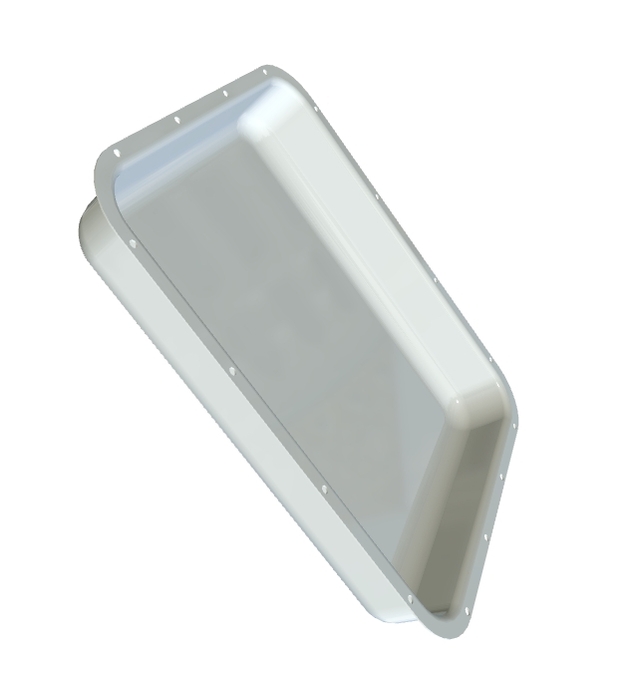
Revolutionize with Innovative Hydroforming Technology
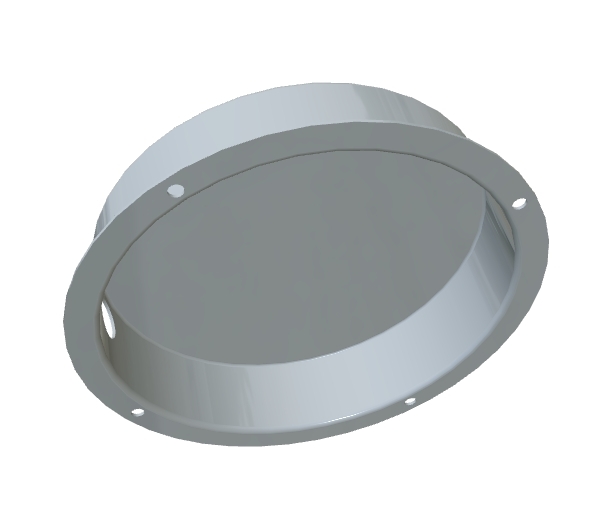
Exploring Hydroforming Technology: Advancements and Applications

Exploring Hydroforming Process: Advantages & Applications
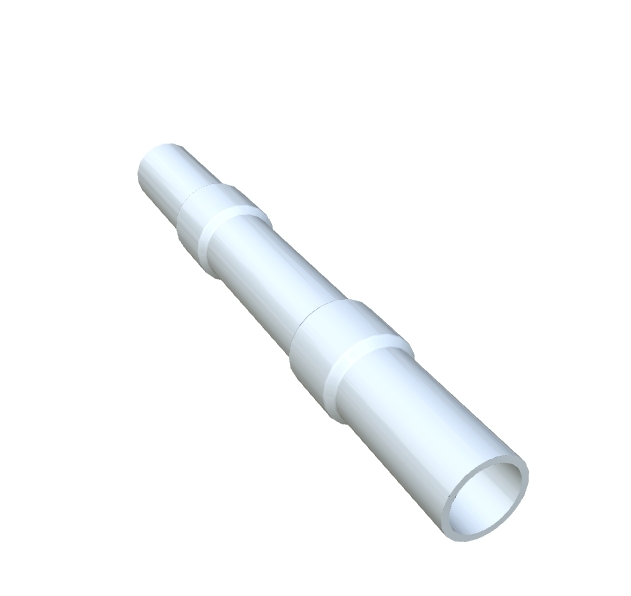
Revolutionizing Part Fabrication: The Hydroforming Process